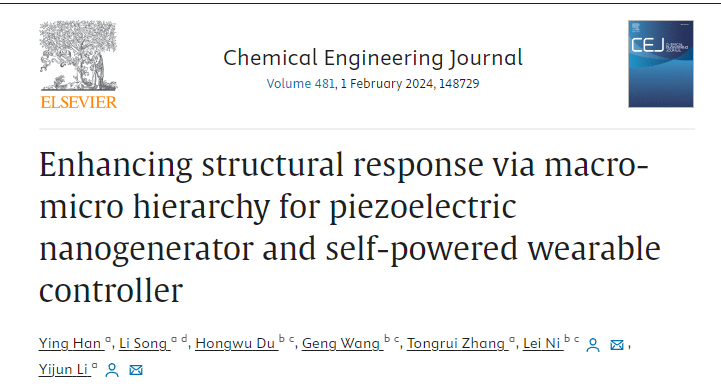
随着柔性电子设备(如触摸屏、柔性显示器和软体机器人)的发展,其独特的灵活性、可穿戴性和适应性引起了广泛的研究兴趣。然而,这些设备普遍依赖外部电源,频繁的电池更换或充电需求限制了其移动性和长时间监控的潜力。鉴于此,压电聚合物复合材料(PPC)以其出色的压电特性、柔性和加工便利性,成为了柔性电子器件自供电的有力候选材料。这些材料能将振动和冲击这样的高熵能转换为电能,实现了有效的传感和动力输出。尽管如此,现有研究多聚焦于PPC薄膜或纤维,未充分挖掘法向形变的潜能。本项研究采用宏微观多层级(MMH)协同设计理念,通过化学发泡辅助熔融沉积成型(FDM)技术,成功制备了PVDF/BaTiO3压电纳米发电机(PENG)。FDM打印不仅能通过宏观结构设计赋予PENG更低的模量和更多的应力集中点以提升形变能力,发泡剂分解在其内部产生的微孔更能通过电晕极化下形成空间电荷驻极体(SCE)显著提升压电输出。本研究重点探讨了三方面:(i)宏观几何设计和微孔结构诱导的多层次结构的影响;(ii)压电驻极体与低模量设计的协同增强效应;以及(iii)该技术在可穿戴电子产品中的潜在应用价值。
课题组李怡俊副教授和西南科技大学倪磊副教授领导的研究团队,运用化学发泡辅助的熔融沉积成型(FDM)技术,成功制备了具有宏微观多层级结构的PVDF/BaTiO3压电纳米发电机(MMH-PENG)。如图1所示,MMH-PENG的制备过程中,化学发泡剂在挤出打印时原位发泡,这一简便而有效的方法能够在材料中形成微孔结构。扫描电子显微镜(SEM)对断面形貌的观察揭示,通过S3M技术,BaTiO3粒子得以在PVDF基体中均匀分散。调控发泡剂的添加比例和FDM打印的温度参数,可在制品中形成不同尺寸(2~180微米)的微孔。这些微孔不仅能够产生应力集中,还能够在电晕极化过程中促进压电驻极体的形成,从而有效提升了材料的压电输出性能。
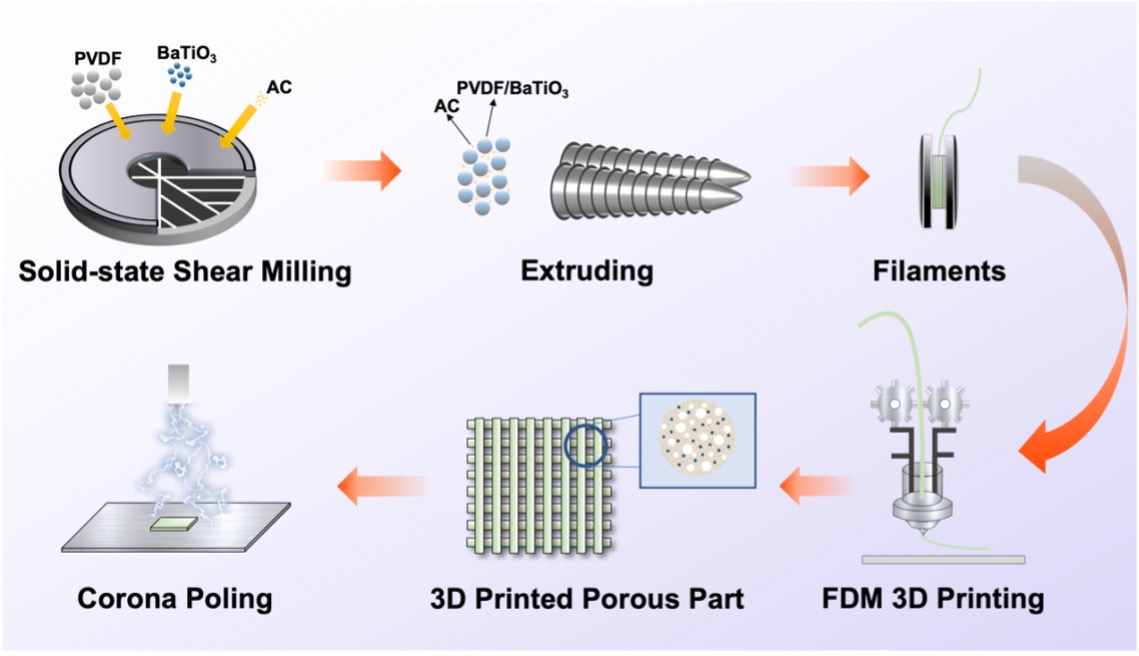
图1. 制备PVDF/BT MMH-PENG的流程示意图
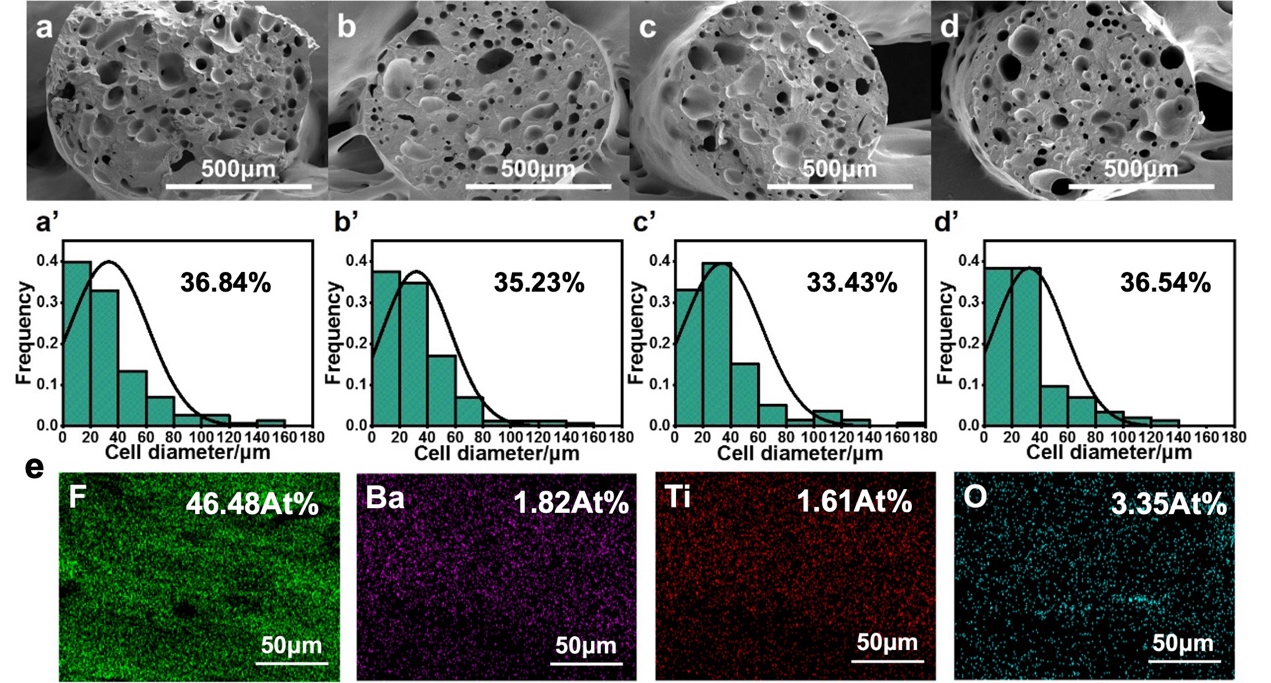
图2. PVDF/BT MMH-PENG的断面形貌和BT分散示意图
首先通过对比不同BT含量MMH-PENG的压电常数d33,介电常数ε,以及开路电压等参数,BT的引入显著提升了材料的压电输出性能。同时,随着BT含量的增加,PVDF/BT复合材料的模量也随之增大。然而,微孔结构的引入有效地缓解了材料介电常数、介电损耗以及模量增加的趋势。实验结果显示,压电驻极体的形成使得材料的开路电压提升了37%。另一方面,通过设计MMH-PENG的整体填充率和表面的应力集中结构,研究揭示了宏观结构和微观结构协同提升PENG压电性能的效果。研究发现,较低的填充率和金字塔型阵列结构能有效降低制品的模量,并在局部区域形成应力集中,从而使压电输出提高52%。因此,在BT含量为20wt%、填充率为0%,且表面呈金字塔型阵列的条件下,MMH-PENG达到了最佳的输出性能,开路电压与短路电流分别为24.5 V和642 nA。
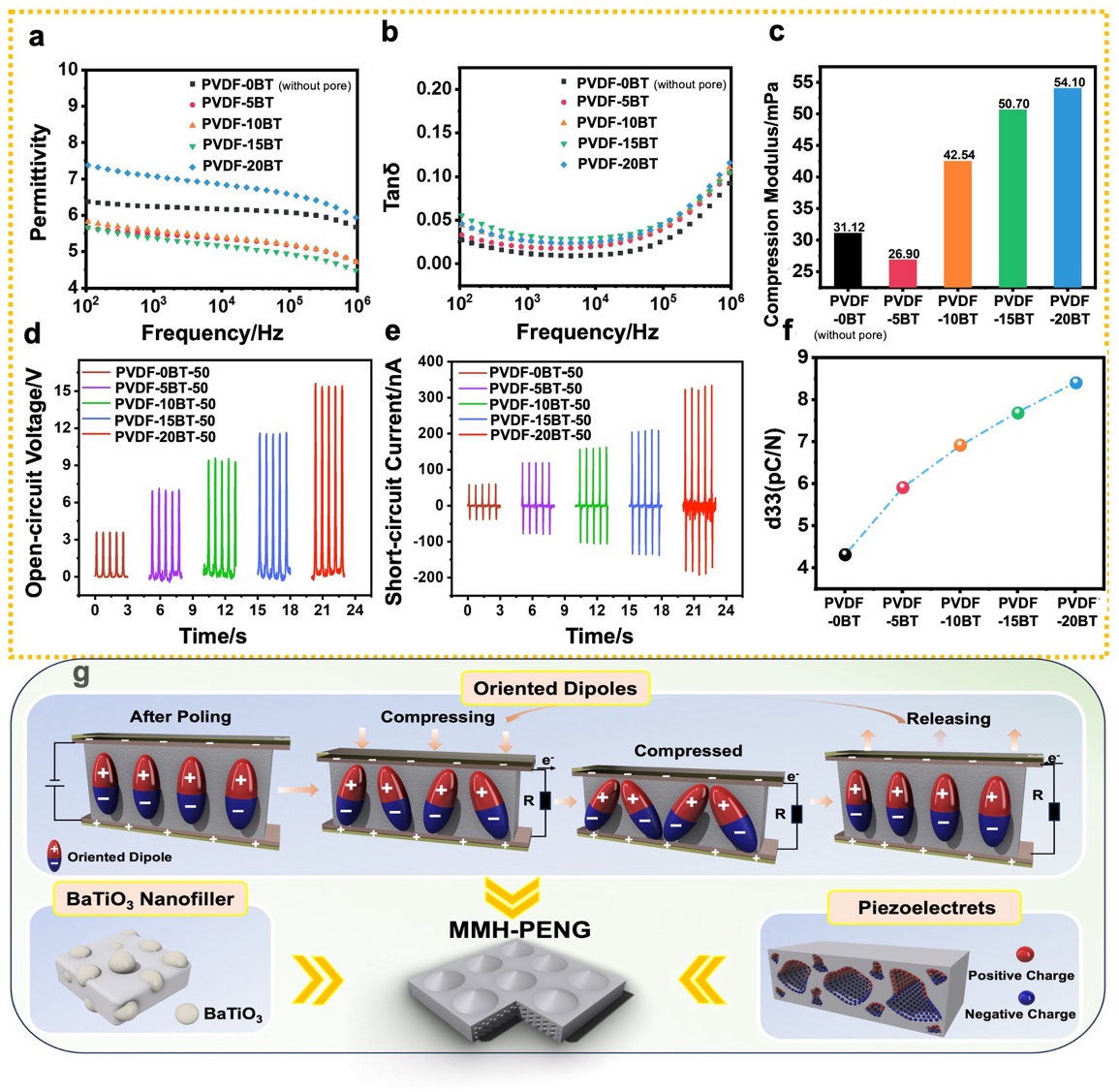
图3、MMH-PENG中不同BT含量的压电性能及影响参数的对比
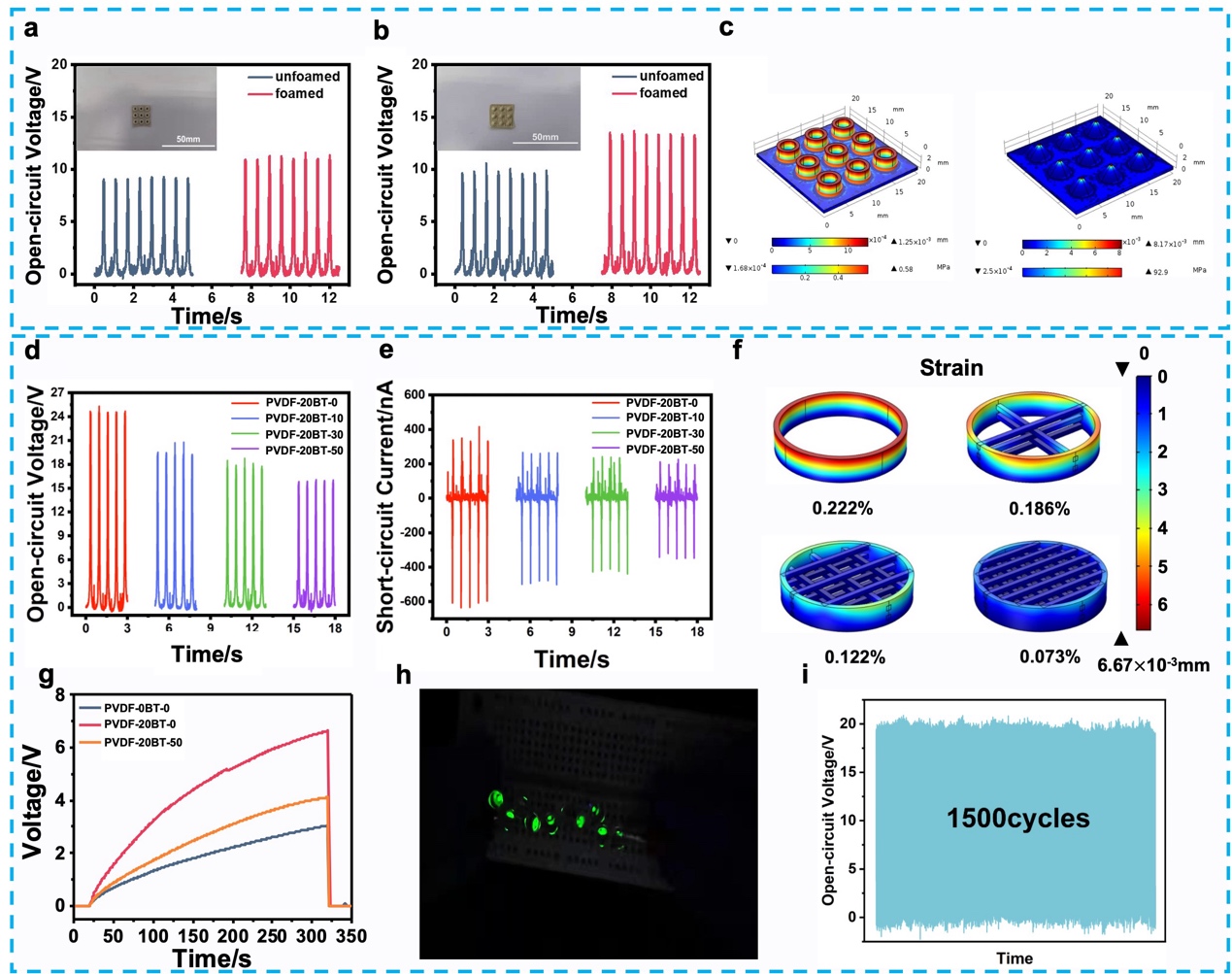
图4、不同宏观结构设计的MMH-PENG的压电性能对比
基于MMH-PENG卓越的性能,本研究成功将其集成于柔性基板,赋予了其出色的灵活性、可调节的灵敏度、便捷的拆装特性以及良好的可重复使用性,这些特点为其在可穿戴设备和自供电控制系统中的应用提供了强有力的支持。实验结果表明,将MMH-PENG应用作为传感器,在增强游戏体验的沉浸感、提升机器人操控的便捷性和精确度方面表现出色,并能在操作过程中实现自我供电。这些特性使得MMH-PENG成为体感游戏控制器和机械臂操作等领域的一个创新选择。
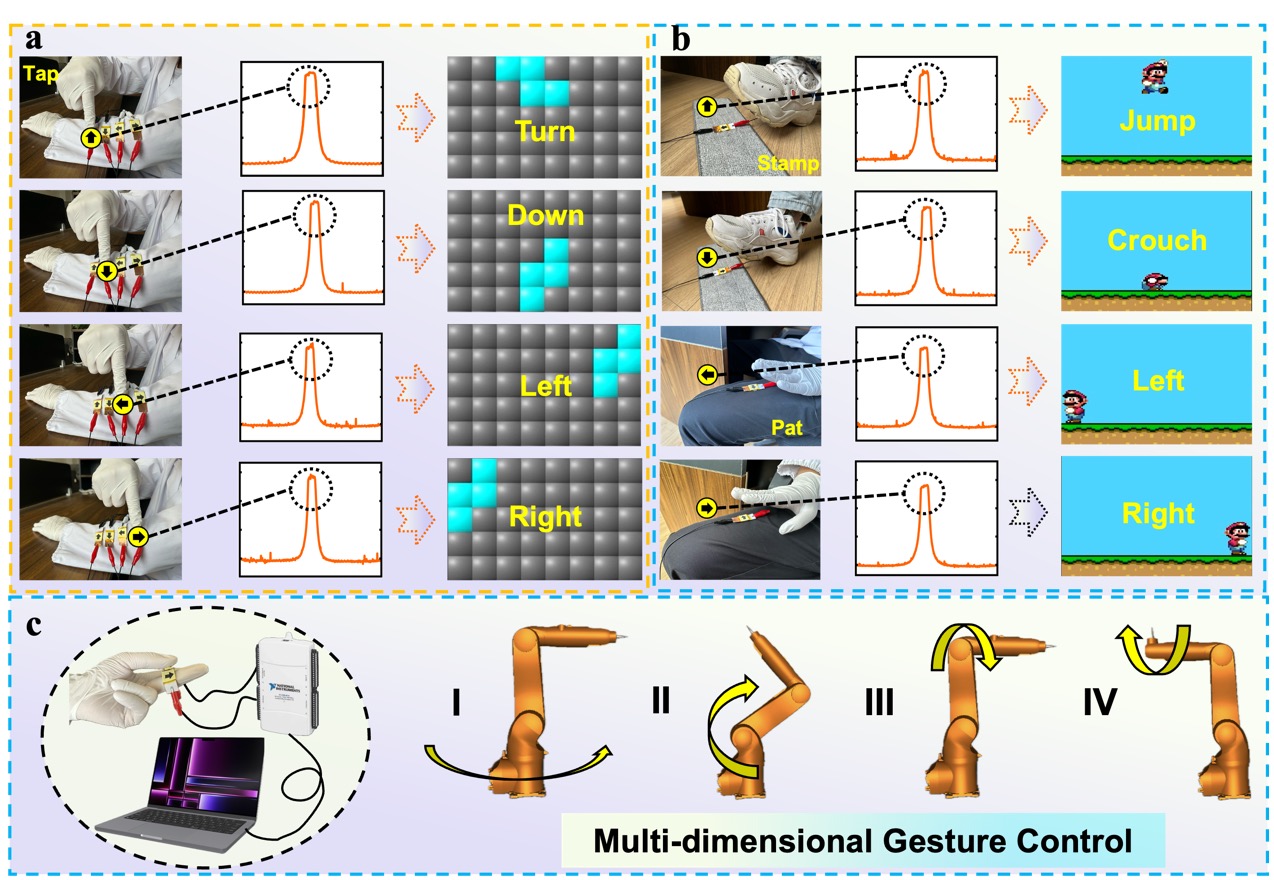
图5、MMH-PENG作为传感器应用与体感游戏以及机械臂操控
综上所述,我们利用原位发泡技术成功制备了具有多孔结构的MMH-PENG。这些大量的微孔结构对减小介电常数ε和促进电荷储存起到了积极作用,特别是在电晕极化过程中,有助于形成压电驻极体。此外,宏微观多层级(MMH)结构设计有效地降低了样品的杨氏模量,从而增强了材料的形变能力,将压电输出提升到24.5 V和642nA。这拓宽了PENG在大规模应用领域中的发展之路,同时为通过多层次结构设计提升PENG压电输出提供了新的思路。
该研究成果以“Enhancing structural response via macro-micro hierarchy for piezoelectric nanogenerator and self-powered wearable controller”为题发表在学术期刊Chemical Engineering Journal上,四川大学大学硕士生韩莹为第一作者,课题组李怡俊副教授和西南科技大学倪磊副教授为共同通讯作者。
原文链接:https://doi.org/10.1016/j.cej.2024.148729